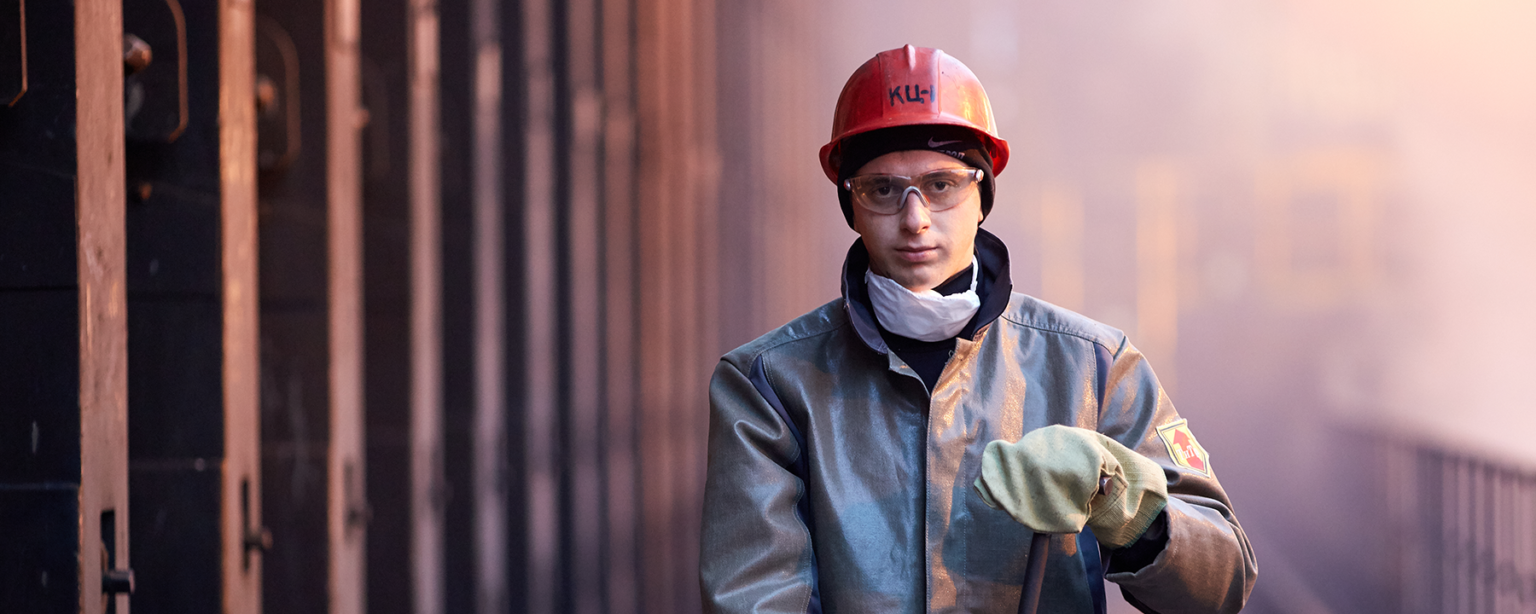
Coke-chemical production
PJSC ArcelorMittal Kryvyi Rih is one of the largest coke manufacturers in Ukraine and Eastern Europe. The plant processes hard coal and produces coke, coke gas and chemical products of coking. ArcelorMittal Kryvyi Rih is the largest consumer of coke-chemical production products. Coke, sulphuric acid and purified coke gas are used in the production cycle of the plant.
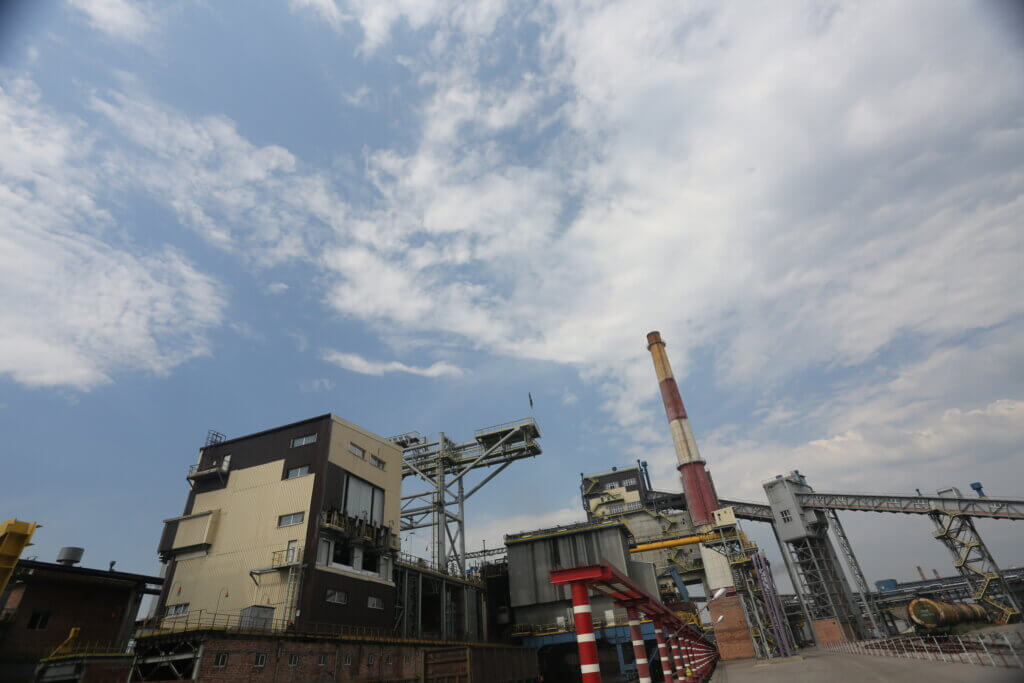
The coke-chemical production facilities include:
- Coal preparation shop. The main task of the shop is acceptance, shipment and storage of coal concentrates, as well as charge preparation and supply to the coal towers of coke shops.
- Coke shop No.1. The shop is designed for coke and coke gas production from coal charge, supplied by conveyor routes of coal feeding from coal preparing shop.
- Recovery shop. The main task of the shop is cooling of coke gas, extraction of coking products from it and its subsequent transfer to desulfurization shop.
- Desulfurization shop. The shop is designed for purification of coke gas from hydrogen sulfide with further production of technical sulfuric acid from hydrogen sulfide gas.
In October 2022, ArcelorMittal Kryvyi Rih decommissioned its oldest coke batteries Nos. 1 and 2. Instead of six coke batteries, there are four left at the company.
Coke batteries No. 1 and 2 with a total capacity of 3 000 tons of gross coke per day were operated for about 50 years and during all wartime months. Shutdown of these batteries was made possible through a phased implementation of the plant's investment program - the construction of new modern units and modernization of the existing ones. Now the production of coke is taken over by high-tech coke batteries No. 5 and 6.
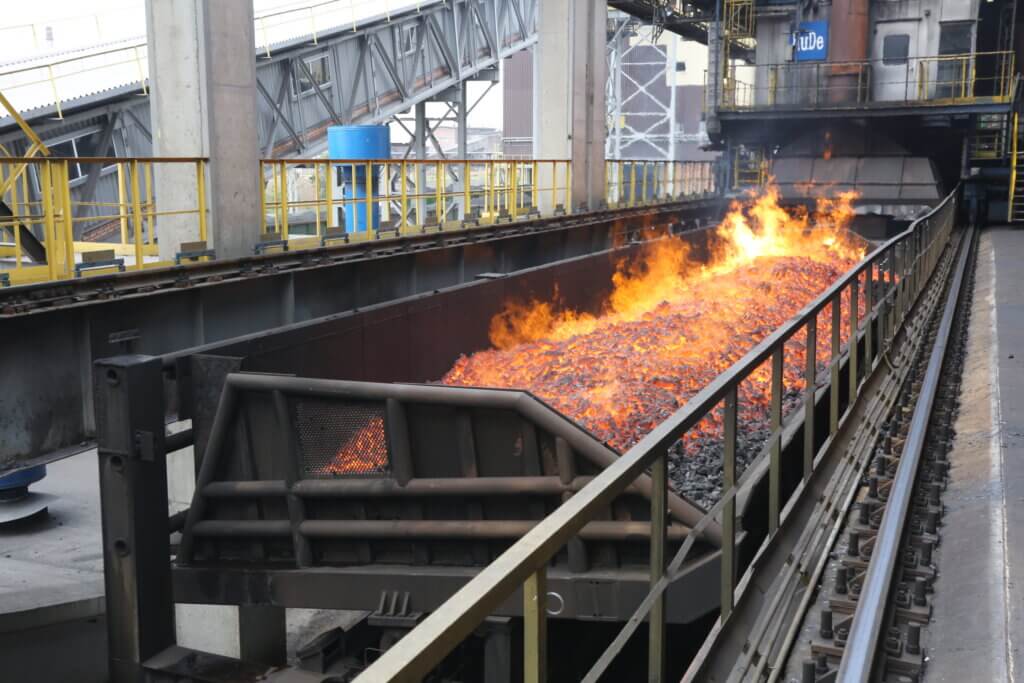
ArcelorMittal Kryvyi Rih is the only metallurgical company in the country that actually built new coke batteries No. 5 and 6 from scratch with a special technical solution that improved product quality and also increased the hot strength of coke up to 55-60%. Construction of these batteries was completed in 2018. The latest technologies to reduce dust and gas emissions were implemented at all stages of coke production - from charging the charge and coking to raw materials dispensing. At the newest batteries, a smokeless loading system of rammed cake with the introduction of the hydro-injection method was implemented; a modern dust-free coke distribution unit was also built. New gas purification units were built at all stages of coke transportation and distribution.
New batteries are more gas-tight, which eliminates gas losses, and the level of dust and gas pollution in the working area has been reduced by 30%. Supply and exhaust ventilation and air conditioning have been installed, which ensures efficient air exchange in the production facilities.
The use of modern technology makes it possible to significantly improve working conditions and workplace safety. Production processes for maintenance of coke furnaces and main process equipment have been automated here, which has significantly simplify work load of coke-chemical employess.