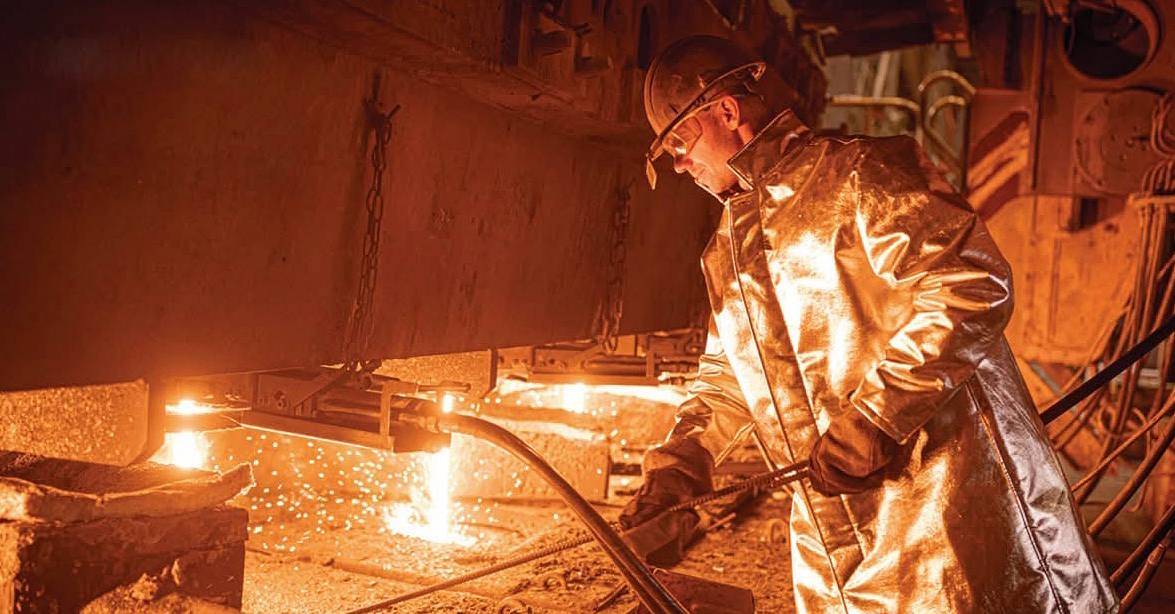
Driving costs down with a record performance
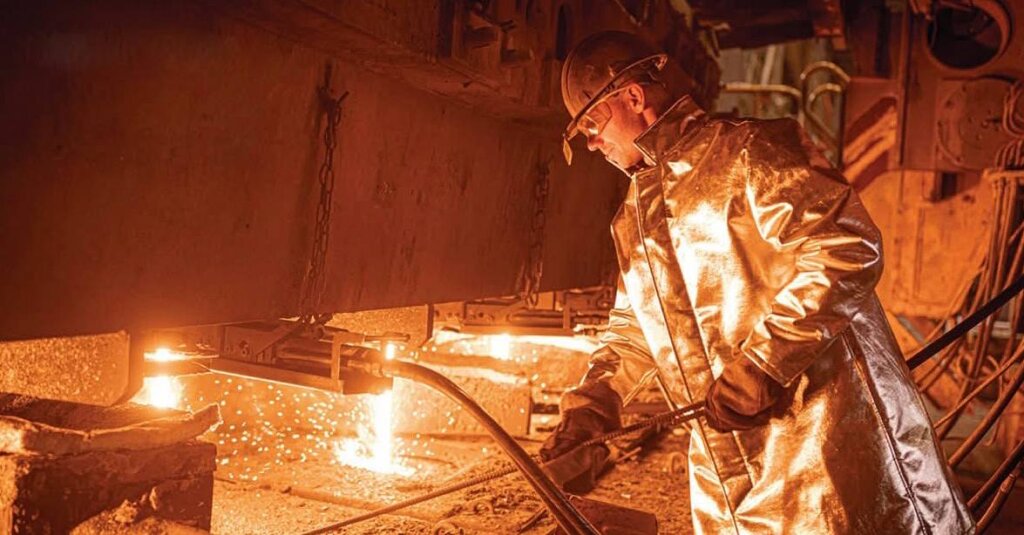
Our steelmakers have once again added to the positive mood and optimism. Despite the problems caused by the full-scale invasion, such as staffing issues, spare parts and materials shortages, blackouts, and poor cooling water quality, they set a new incredible record of 70 heats in a sequence on continuous casting machine No. 2 at BOF Shop. Increasing the number of heats in sequence is extremely important, as it reduces the cost of steel billets used to produce rolled products, which are in demand on the market. The cost is reduced by decreasing energy and materials consumption as well as wastes generation.
As noted by Kyrylo Chmyrkov, deputy head of BOF Shop for steel secondary treatment, the significant achievements of LFCC in increasing the number of heats per sequence are the result of teamwork between casting operators, steelmakers of steel secondary treatment unit, refractory men, repairmen, operators, crane operators, BOF team, specialists from Technical Department, and Iron and Steel Making Department, and many other employees.
"The record sequence lasted for 65 hours. This means that approximately 200 employees of LFCC and other subdivisions of BOF Shop from all four teams participated in setting the record,” says Kyrylo Chmyrkov. “The latest records and the increase in number of heats per sequence in general show that our team has achieved results in improving the reliability of tundishes.”
The tundish consists of a metal body lined with refractory materials that protect the body from high temperatures (the steel in the tundish has a temperature of at least 1 480 degrees Celsius). Steelmakers are working together with Technical Department to improve the life of the lining and prevent the body itself from overheating.
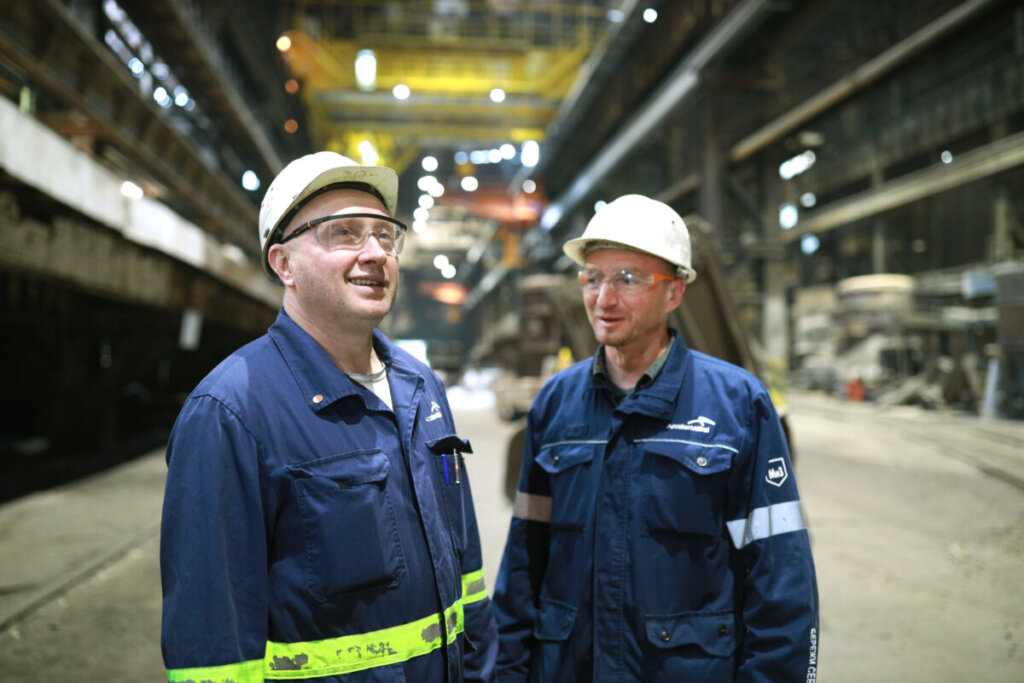
“We are solving these problems step by step. We study, research, implement measures, and test them in practice,” explains Serhii Slipchenko, lead engineer of Technical Department. “It was this set of measures that yielded results. To ensure the reliability of the tundishes, the design of the lining was changed, more reliable gunning materials were selected, overheating zones were reinforced, insulation between the protective layer and metal structures was improved, and so on.”
Dmytro Levytskyi, senior foreman of refractory section of BOF Shop, added that the lining scheme had to be changed to increase reliability.
“For protection, we cover the tundishes from the inside with refractory gunning body,” explains Dmytro Levytskyi. “At first, we covered the most problematic areas, which are prone to burnout, with protective refractory plates. Then we tried to install such plates over the entire surface. And it worked; the service life of the lining was extended.”
Kyrylo Chmyrkov added that a new system for measuring the temperature of steel in the tundish is being implemented. It is automatic, and the measurements do not put additional pressure on the lining, as was the case with manual measurements. The steel casting operators receive data practically in real time, which makes it possible to change the casting parameters in a timely manner. All this has not only allowed us to set records, but also to increase the average number of heats per sequence. For example, if in 2021 we had an average of 23 heats per sequence, in 2025 we plan to have 33. And so far, everything is going according to plan.
Continuous casting, as the name suggests, is a continuous process. Therefore, all LFCC equipment, from steel secondary treatment units to cooling beds, must operate without forced stops. This is a prerequisite for achieving high sequence rates. The repairmen of LFCC are constantly working on this.
“In recent years, our repair service has been reorganized taking into account global experience,” says Mykola Yefimenko, head of the LFCC equipment maintenance and repair service. “We have a new position – technician. So now we have more eyes, which allows us to preventively identify defects and eliminate them in a timely manner. We work closely with technologists, which also has a positive impact on the condition of the equipment. There are plenty of challenges. Many of them are related to the consequences of the full-scale invasion, such as a shortage of spare parts. But despite this, we have managed to stabilize the operation of the equipment.”
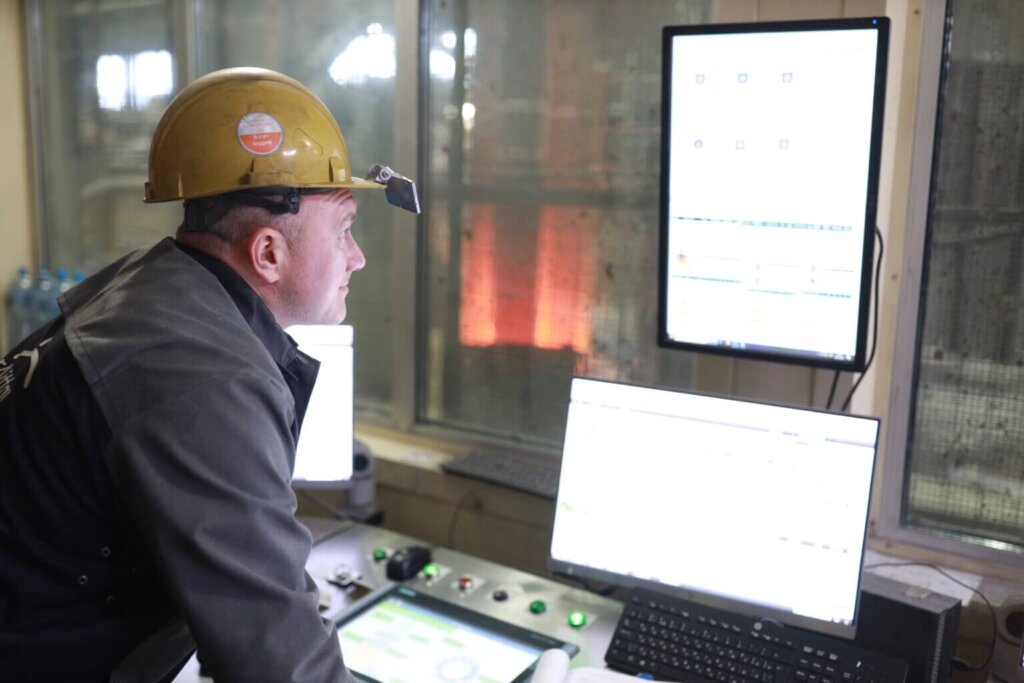
Much depends on the quality and speed of steel treatment in the ladle furnace unit. “We need to get steel with precise chemical composition and temperature parameters, and we need to do it quickly,” says Andrii Bakun, a steelmaker of steel secondary treatment unit. Because if a steelmaker does not manage to refine the heat within the specified time, the sequence will have to be terminated. The most important thing for a steelmaker is to calculate the chemical analysis correctly. The mistake comes at a high price.”
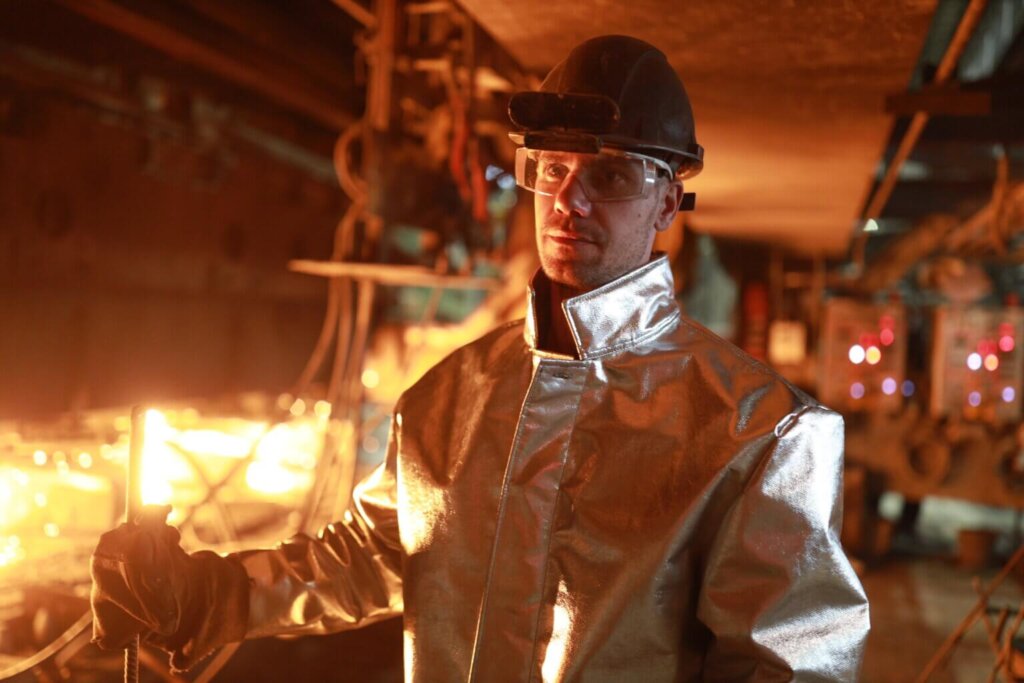
Andrii Marchuk, acting senior steel casting operator of continuous casting machine, organizes the work of the team that prepares the continuous casting machine and casts steel. The sequence also depends on his decisions. “My task is to organize the team of steel casting operators, clearly assign tasks, get people ready for work, and make sure that everything is done,” says Andrii Marchuk. “Steel casting operators also must prepare the equipment for the sequence flawlessly. Because if there are mistakes or negligence during preparation, the sequence is doomed before it even starts.”
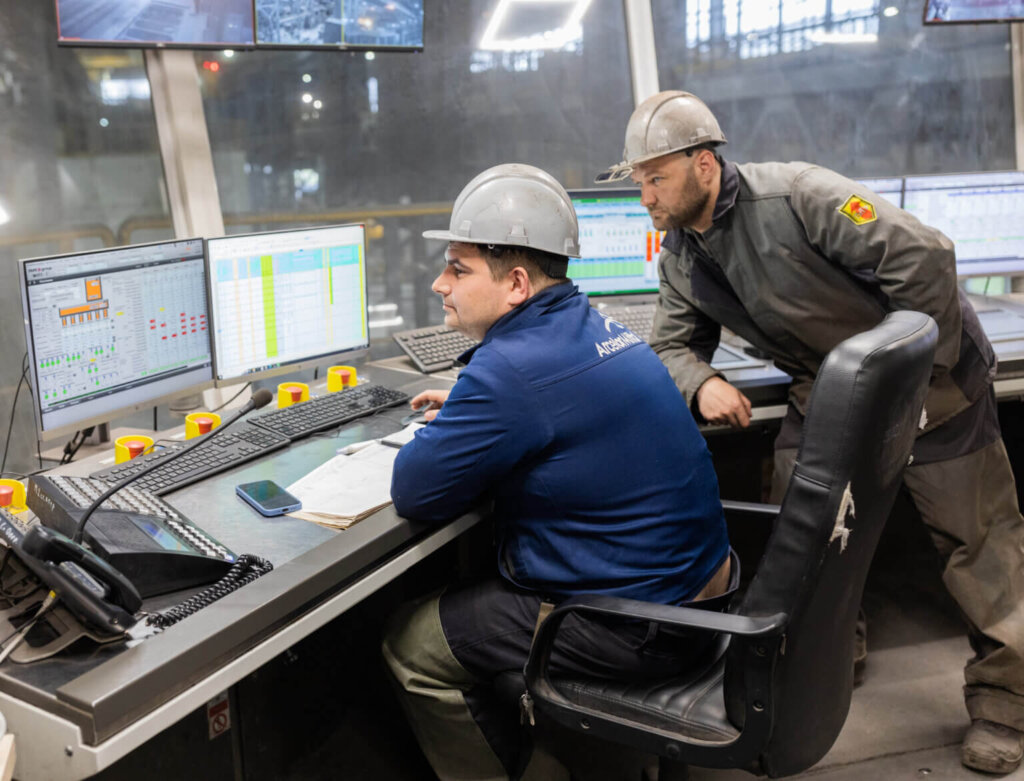
Tymofii Zhmaka is a senior operator of the CCM-2 control room. He is the one who sets the temperature and speed for casting. “I see all the information I need to control the casting process on my monitor,” explains Tymofii Zhmaka. “It is very important for an operator to respond promptly to any unexpected situations, such as when the backup tundishes are cold, or the steelmaker is unable to bring the steel to the required parameters in time. It is the operator's experience and skill that will allow the situation to be corrected.”
Andrii Kukhta is a flame cutting torch operator. He works with a flame cutting torch but associates his work with that of a firefighter. “As long as everything goes according to the plan, the billets are cut to a specific length automatically. But if something goes wrong, we get to work and cut manually, using torches. It is important for us not to lose our vigilance for a moment and to complete the work on time so as not to lose the sequence.”
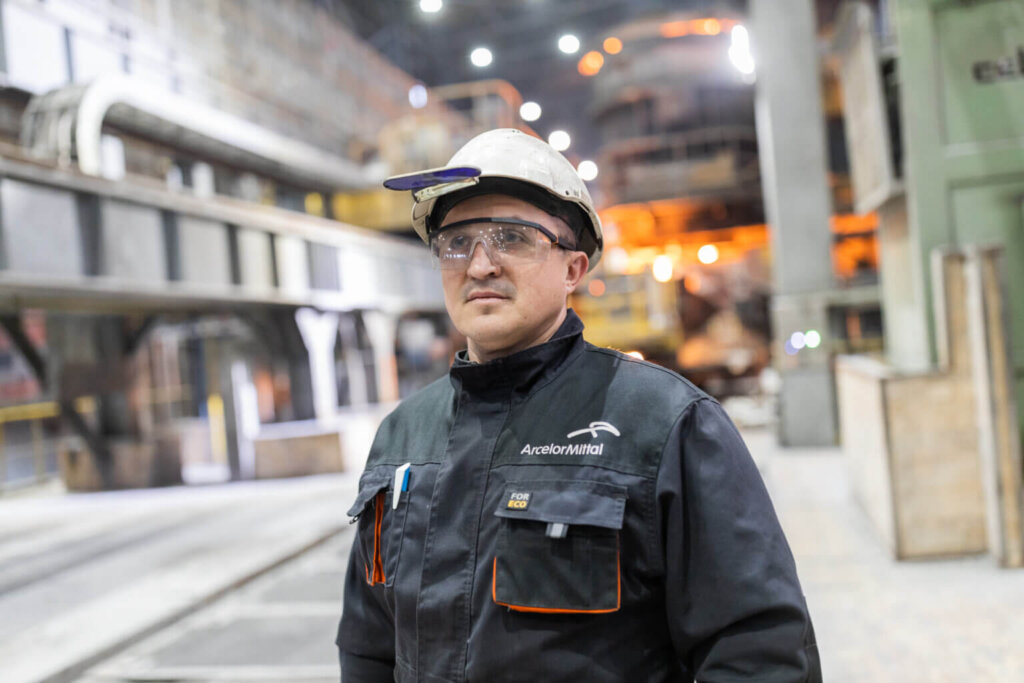
A shift foreman manages the operation of all three continuous casting machines. Today, that person is Oleksandr Yatsenko. “If everything goes according to the schedule, there are no complications,” says Oleksandr Yatsenko. “But there are times when the heats arrive late. Or, vice versa, the ladles with steel have already arrived, but we are still casting the previous heat. And it is me who makes the decision: to speed up the casting or, on the contrary, to slow it down. And the correctness of those decisions also determines how long the sequence will last. I want to thank each of my colleagues. Equipment is important. But it is people who set records.”